Much like the pilot or prototype stage, the cost drivers are time plus materials. Because the equipment is much larger, the material requirement is also much larger. Our guidance to our clients is to err on the high side for the estimate of material required. When running a new construction for the first time on production equipment, we can never be sure of the result. By design, a production trial is a very short run involving new setups and many untested process variables. Therefore, it is highly cost effective to plan on having ample material for startup and to define the process versus trying to be conservative to save on material cost. The least optimal scenario is to spend a great deal of time and material lining out the new process only to run out of material once samples have been saved.
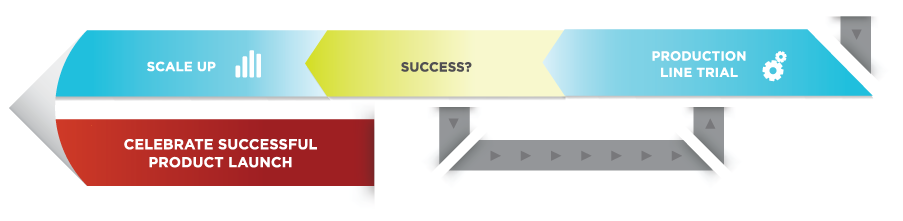
In such cases, another trial must be scheduled, resulting in a doubling of cost. Generally, we recommend that our clients plan to have at least 2,500 lbs. for each material. While it can take up to 1,000 lbs. to line out, we can usually slow down the output rate and obtain production scale prototype rolls and laminations for our clients’ field trials and the testing that’s required for qualification. Sometimes a client will want to evaluate different variations to their product or construction in the trial. For each gauge or color change made in a production trial, an additional 500 lbs. of polymer is recommended. Our vast experience has shown that many variations in a production trial can greatly increase costs. This is why we recommend the pilot line process to answer as many questions about the extrusion materials and construction as possible. The range on raw material pricing can vary greatly. Most thermoplastic resins will cost between $2.00 and $6.00 per pound, however we produce many specialty products, for which the materials cost less than $10.00 per pound. With an idea of the amount of polymer needed, you can estimate how much this will cost for each production trial.
The time portion of the equation is comprised of the setup, the actual extrusion, and the cleanup. Depending on the complexity and uniqueness of the trial, the setup can be a highly-involved process. Sometimes modifications to auxiliary equipment need to be made and new web paths need to be created. The time required for a production trial from the time we start the setup work to the time when we are done the cleanup and the tear down is 24 hours. Because we cannot recover the cost of this full amount of time from our clients, we charge a flat fee for setup and we charge by the hour for extrusion time with a minimum amount of extrusion time of 8 hours. If a client needs many different variations, there are circumstances when more than 8 hours is needed – in cases such as these, we increase by 1 hour increments. A normal production trial time component will cost our clients $20,000 to $25,000. This cost helps to partially offset Bixby’s lost production time. If there is significant amount of process development to be done, Bixby will develop a plan with our client to make sure that expectations are established and are agreed upon, and that costs are allocated appropriately. By doing this, we are confident we can deliver the client’s objectives in the production trial phase.
Under the parameters outlined above, what does the client receive?
- Sufficient production quality parts to:
- Meet the qualifications that are required at this level
- Scale up of downstream processes
- Use for sales and marketing samples
- A fully scalable production process
- Additional test data from Bixby’s lab if required
- Confidence that the system is developed to support the launch of a new product
Under the parameters outlined above, what does the client receive?
- Sufficient production quality parts to:
- Meet the qualifications that are required at this level
- Scale up of downstream processes
- Use for sales and marketing samples
- A fully scalable production process
- Additional test data from Bixby’s lab if required
- Confidence that the system is developed to support the launch of a new product
How long does it take to complete this process?
New product development is Bixby’s growth engine. As such, we have dedicated line time in place each month for production trials. This is supported from the very top of the organization. As outlined above, production extrusion trials are costly to our clients as well as to Bixby. We view this as an investment in our future. Because dedicated line time is set aside monthly, if the raw materials are available then the longest our client will wait to get a trial done is four weeks.
However, if there is longer lead time equipment required, then the schedule will be impacted. If we make the conservative assumption that it will take three iterations to perfect the process, and the client can turn around its testing very quickly, then the production trial and scale-up phase could be done in about 12 weeks. We know from experience with our clients, many of whom had engaged other extrusion companies before calling on Bixby, that this is an extremely fast turnaround time, compared to industry standards.